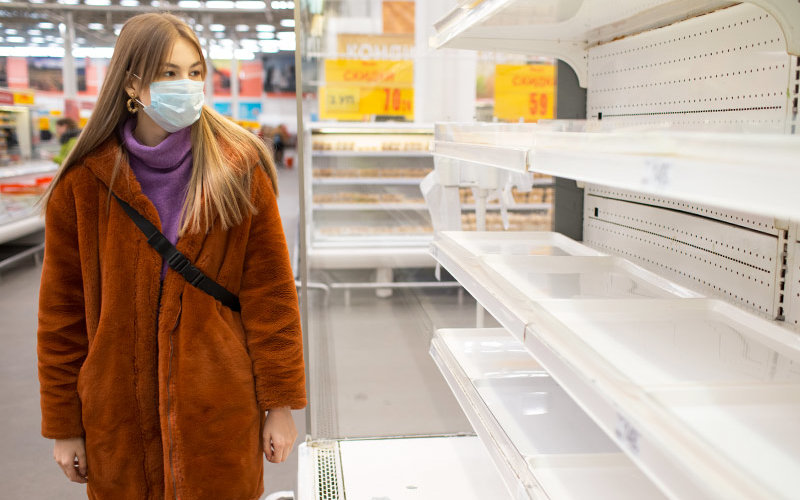
Americans inevitably have seen or heard about empty store shelves and the rationing of toilet paper amid the COVID-19 pandemic. While people have been panic-buying and hoarding in response to the global health crisis, the situation also begs the question: Is there something inherently wrong with the supply chain?
Not really, said Min Choi, assistant professor of management and supply chain management expert at Cal State Fullerton. Although the current crisis is exposing its weaknesses, “the pandemic actually presents an opportunity for businesses and supply chain management professionals to rethink their priorities,” she said.
As business has globalized over the past 30 years, many companies have prioritized low cost, streamlining manufacturing and sourcing overseas to produce more efficiently and cheaply. Supply chains have become “stretched out” — meaning that the flow of materials, information and financial resources to deliver products to the right place, at the right time, in the right quantities gets complex, involving multiple companies across country borders.
Some chains can seem downright absurd. Choi cites cases where a product is designed in the U.S., parts manufactured in China and delivered back to the U.S. to be assembled into finished goods and shipped back to China for sales. “Yes, the carbon footprint is higher,” she admitted, “but it’s still cheaper sometimes to deliver it this way, and that’s been the priority for many supply chains.”
The result is that consumers have enjoyed cheap goods and companies have profited. However, when disruptions occur, the complicated supply web leaves companies vulnerable. “And they are even less able to mitigate this when the disruption is worldwide,” added Choi.
In the past few years, a push to shorten supply chains has begun, mostly in the name of sustainability (think farm-to-table and “buy local” movements). Choi believes that companies’ risk exposure, as demonstrated by the COVID-19 pandemic, is another reason to do so. She expects a shift to less interdependency, greater flexibility and even more localized production.
One way to gain greater flexibility is to offer more products and services through the online channel. “This was already a trend, but the new coronavirus expedited it,” Choi explained. “A clear example is education. Online learning had been growing, but the crisis forced a switch in a matter of weeks.”
A lack of flexibility, said Choi, is why it has been difficult to keep toilet paper in stock. “Industries like ice cream or pool supplies are used to seasonal demand changes and are ready for that to some extent. In the pandemic, demand has skyrocketed for items with traditionally stable demand throughout the year: toilet paper, wipes, masks. Such companies are not used to fluctuations and their production lines aren’t prepared for that.”
While there’s no simple solution to supply chain problems, Choi foresees companies using learnings from the COVID-19 crisis to better balance cost and flexibility priorities, allowing them to be more resilient in future disruptions.
Contact: Karen Lindell, klindell@fullerton.edu